Table of Contents
In industrial non-destructive testing (NDT), precision and repeatability are critical. An XY scanner—also known as a dual-axis scanner or index scanner—is a tool that enables detailed surface and subsurface inspections by automating scan paths across two perpendicular axes. Whether you’re working in aerospace, oil & gas, or infrastructure maintenance, these scanners are crucial for identifying corrosion, defects, or inconsistencies in metal structures.
What Is an XY Scanner?
An XY scanner is a mechanical system designed to move a scanning probe along both the X and Y axes. This movement allows for a raster-style scan over a flat or curved surface, capturing high-resolution data for defect detection or thickness mapping. Paired with an ultrasonic or phased array probe, it becomes a complete corrosion mapping scanner.
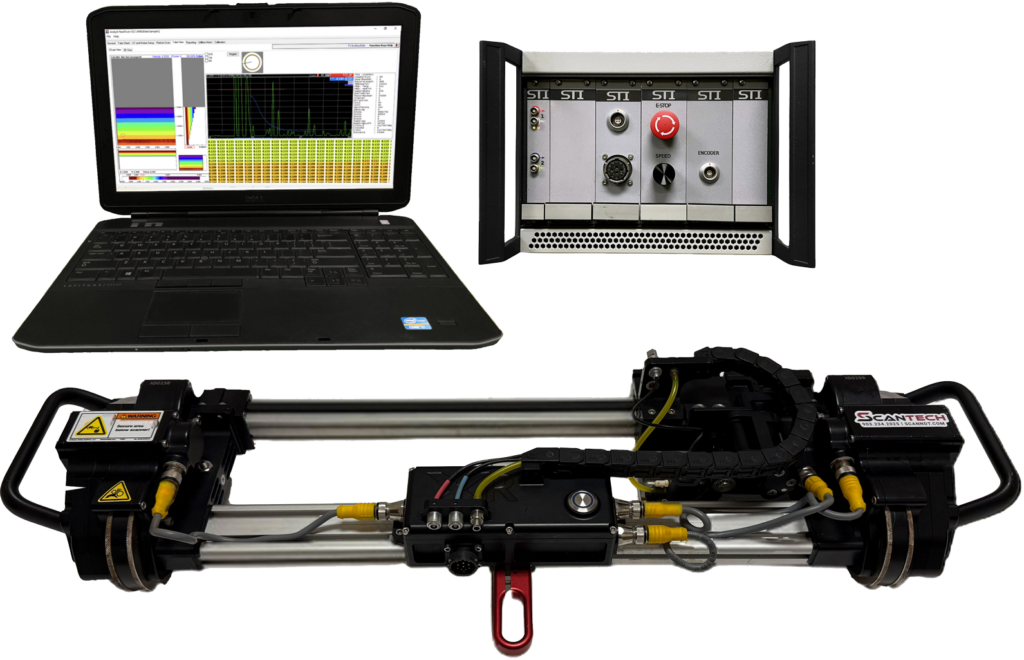
Common Names for XY Scanners:
- Dual-axis scanner
- Corrosion mapping scanner
- Corrosion mapper
- Index scanner (especially in phased array setups)
Applications: Corrosion Mapping and Beyond
The most common use of an XY scanner is in corrosion mapping—particularly for pipelines, storage tanks, and ship hulls. Using ultrasonic waves, the scanner creates a thickness map of the scanned area, identifying internal corrosion that may not be visible on the surface.
When paired with a corrosion mapper or data acquisition software, the system can:
- Detect wall thinning
- Map corrosion spread over time
- Help prioritize maintenance actions
- Catch failures before they happen.
Understanding Raster Scan and C Scan Imaging
A key strength of the XY scanner is its ability to perform raster scans—moving the probe in a zigzag pattern to cover the entire surface. This ensures that no area is skipped and results in consistent, repeatable data.
The data output is typically shown as a C scan—a top-down 2D image that reveals thickness variations, voids, or corrosion zones. Think of it as an ultrasound image for metal.
XY Scanner vs. Index Scanner vs. Manual Mapping
How an XY Scanner Enhances Corrosion Mapping Workflows
In modern NDT workflows, efficiency and data integrity are everything. Integrating an XY scanner into your corrosion mapping process doesn’t just automate the scan—it improves the entire workflow from inspection setup to reporting.
Here’s how:
1. Automated Precision
Manual inspections rely heavily on the operator’s consistency. XY scanners automate scan paths across both axes, ensuring that every square inch of the surface is covered systematically—ideal for detecting pitting, wall thinning, and corrosion clusters.
2. Repeatability for Baseline Comparisons
When inspecting the same asset over time (e.g., pipelines or tanks), you need to ensure your data is coming from the same exact location each time. An XY scanner allows you to reproduce the scan with millimeter-level accuracy—critical for baseline comparison and lifecycle monitoring.
This level of repeatability pairs well with advanced reporting tools. Learn more about our ultrasonic testing software integration designed to simplify corrosion data management.
3. Faster Scans, Richer Data
Thanks to automated raster scanning, large surfaces can be mapped much faster than manual methods. Combine that with C-scan output, and you’re not just collecting data—you’re creating a visual corrosion map that’s easy to interpret and report.
Choosing the Right Corrosion Mapping Scanner
When selecting an XY scanner or corrosion mapping scanner, consider:
- Surface area: Larger scanners cover more in one go
- Resolution: Higher step resolution means finer detail
- Environmental conditions: Need waterproofing? High-temp durability?
- Software compatibility: Does it work with your ultrasonic gear or corrosion mapper software?
Top Applications for an XY Scanner
1. Storage Tanks and Pressure Vessels
-
- Why it’s ideal: Large surface area, often flat or cylindrical
- Scanner advantage: Provides full coverage corrosion maps in raster patterns
- Industry: Oil & gas, chemical plants, refineries
- Bonus: Compatible with ASME B31G analysis for remaining strength evaluation in corroded pipelines—fully supported by our XR software.
2. Pipelines (Above-Ground, Horizontal Runs)
-
- Why it’s ideal: Long, straight segments = perfect for dual-axis scanning
- Scanner advantage: Detects wall thinning, pitting, and general corrosion with precision
- Industry: Petrochemical, natural gas, water utilities
- Bonus: Pairs well with phased array ultrasonic probes for weld inspection too
3. Ship Hulls & Marine Structures
-
- Why it’s ideal: Large, slightly curved metallic surfaces exposed to harsh environments
- Scanner advantage: Detects corrosion due to saltwater exposure, supports drydock planning
- Industry: Maritime, offshore platforms, naval maintenance
4. Aerospace Structural Panels
-
- Why it’s ideal: High-precision inspection on composite or metal panels
- Scanner advantage: Maps delaminations or corrosion under riveted skins
- Industry: Commercial aviation, defense contractors, aerospace OEMs
Why XY Scanners Are Essential in NDT
In today’s industrial environment, the cost of failure is too high. XY scanners offer a reliable, repeatable, and precise way to detect corrosion, map flaws, and maintain safety. Whether you call it a dual-axis scanner, an index scanner, or a corrosion mapper, this tool plays a critical role in modern non-destructive testing.